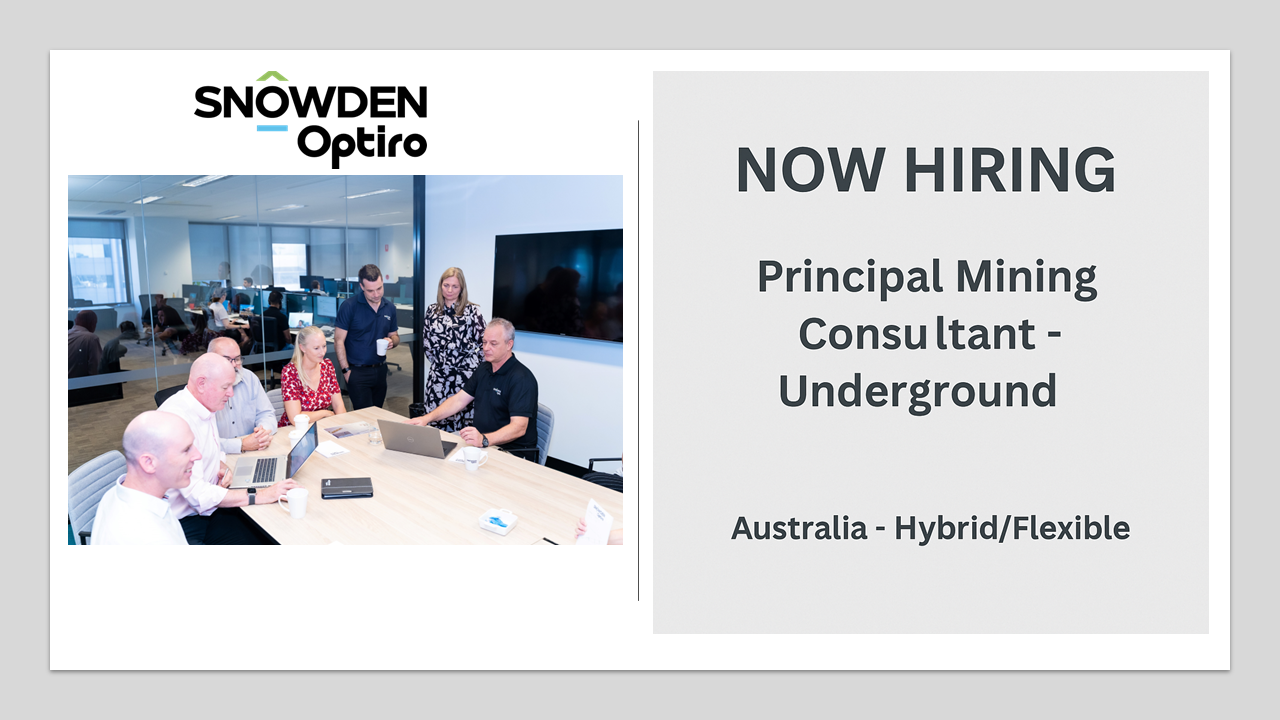
- news
Unlocking the mine value chain: A detailed look at transitions from resource model to final product
Rayleen Hargreaves, Principal Consultant and Reconcilor Product Owner at Snowden Optiro provides detailed insights into unlocking the mining value chain and breaks down its key stages.
The mining value chain is a multifaceted process that begins with the initial resource model and culminates in the production of the final product, whether it’s concentrate or dore bars. Each stage along this journey brings its own complexities, challenges, and opportunities for optimisation. To effectively manage and maximise recovery, the key to success lies in maintaining a robust reconciliation process at every step.
In this blog, we’ll explore the critical stages of the mining value chain and how reconciliation plays a crucial role in ensuring operational accuracy, transparency, and financial sustainability.
The Resource Model: Establishing the foundation for mining operations
The mining process begins with a resource model, which provides an estimate of the total quantity and quality of mineralised material in a deposit. This model encompasses both potentially mineable and non-mineable material. It is based on geological data, classifying material based on certainty and grade, but it does not yet account for economic, technical, or practical mining constraints.
Reconciliation insight: Reconciliation at the resource model stage focuses on adjusting early assumptions as more data becomes available. It ensures that the geological assumptions and confidence levels (e.g., Measured, Indicated, Inferred) remain valid. As data density increases, reconciliation allows for the reclassification of material, improving the overall reliability of the resource estimate.
Transition to the Reserve Model: Adding realism to resource estimates
As the project progresses, the transition from the resource model to the reserve model brings more clarity. With the inclusion of additional drilling data, the reserve model offers a more precise estimate of the ore-waste boundary, factoring in mining constraints, recovery rates, and updated cut-off grades.
Dilution and recovery must now be incorporated, as they were not considered in the resource model, leading to adjustments in tonnage and grade expectations. Operational constraints, such as access, also play a crucial role in determining the material that is economically viable for extraction.
Reconciliation insight: Regular reconciliation between the resource and reserve models is vital for identifying and addressing inconsistencies as more data becomes available and conditions evolve. By comparing the models continuously, operations can adjust for factors such as dilution, ore loss, and market changes, refining production forecasts and improving the accuracy of economic projections. This process ensures the mine plan aligns with real-world extraction conditions.
The Grade Control Model: Navigating short-term variability
With the reserve model in place, operations move to the grade control model, which is typically developed from higher-resolution data, such as blast hole drilling. This stage focuses on real-time adjustments and short-term planning, fine-tuning ore-waste boundaries and cut-off grades based on current mining conditions.
The grade control model enables more selective mining by providing detailed guidance for excavation and blasting decisions. Continuous reconciliation between the grade control, reserve, and production models allows operators to refine their strategies, minimising ore loss and managing grade variability.
Reconciliation insight: At this stage, reconciliation is crucial for short-term mine planning. By comparing the grade control model with actual production results, operators can quickly detect deviations in grade, ore-waste differentiation, or precision in excavation. Early identification of these issues allows for immediate adjustments, improving operational efficiency and ensuring alignment with production goals.
Mine Production: Turning plans into action
As mining operations ramp up, precision becomes critical for executing the mine plan smoothly. The grade control model provides the high-resolution data needed to make informed decisions about excavation boundaries, blasting designs, and material handling. This ensures ore is properly differentiated from waste and sent to the correct locations.
The challenges at this stage are significant. Ore-waste differentiation must be exact, requiring constant adjustments based on short-term variability. Additionally, material blending and stockpiling strategies must be optimised to maintain a consistent plant feed, which is essential for maximising recovery rates and maintaining steady production. Inconsistent grade or material composition can disrupt processing efficiency, leading to lower metallurgical recovery and bottlenecks.
Reconciliation insight: Reconciliation tracks the alignment between planned and actual production, allowing operators to identify inefficiencies in real time and make quick corrections. This ensures that production targets are met, ore losses and dilution are minimised, and material is sent to the correct destinations. This ongoing feedback loop is critical for operational efficiency and staying within financial and recovery goals.
From Mine to Crusher: Maintaining material integrity
The transition of material from mine production to the crusher brings additional challenges, particularly in handling and transport. Ore losses and dilution can occur during haulage, and calibration errors in weightometers can result in inaccurate measurements. Crusher efficiency, material selection, and stockpiling also affect the quality and quantity of material fed into the plant.
Stockpiling presents a significant risk during this phase. Although it helps maintain a consistent feed to the crusher, improper stockpiling can cause material segregation, where different grades or ore types separate, affecting the consistency of the plant feed. Additionally, extended stockpiling can lead to oxidation, material property changes, or fine material loss through dust, all of which degrade feedstock quality.
Reconciliation insight: Reconciliation at this stage ensures that the material fed into the crusher matches expectations in terms of grade, weight, and moisture content. By identifying material losses or inefficiencies in handling, reconciliation allows corrective actions to be taken before the ore reaches the plant, improving process efficiency and optimising material quality.
Plant Feed: Grinding, recovering, and upgrading
Once the ore reaches the plant, the focus shifts to maximising metal recovery. This stage involves grinding, separating valuable minerals, and upgrading material to produce concentrate or dore bars. Metallurgical recovery efficiency is critical to minimising losses to tailings.
Accurate plant feed data is essential for effective tailings management and metal recovery. Discrepancies between expected and actual plant feed data can result in inefficiencies that affect the entire recovery process.
Reconciliation insight: At the plant feed stage, reconciliation ensures that ore processing performance aligns with expectations from earlier models. It is the final opportunity to capture inefficiencies and adjust processes, maximising the recovery of valuable metals.
Final Product: Ensuring quality and transparency
At the end of the value chain, the final product, whether it’s concentrate or dore bars, must meet quality standards for shipment or sale. Sampling and assaying are crucial for verifying grade, while moisture removal ensures the product meets transportation requirements.
Reconciliation insight: Reconciliation of the final product ensures that the overall recovery rate aligns with expectations, highlighting any inefficiencies from earlier stages. It also provides financial reconciliation, confirming that revenue matches the projected output.
Conclusion: Why reconciliation is the key to mining success
Throughout the mining value chain, reconciliation serves as the vital link between models, predictions, and actual performance. It identifies inefficiencies, optimises processes, and enhances transparency—critical factors for the financial health and sustainability of mining operations.
For a more detailed visual representation of the changes that occur between each node of the mining value chain, check out our infographic on the mining value chain below:
This infographic outlines some of the key transitions and challenges from the resource model to final product, helping you understand the critical points where reconciliation plays a pivotal role.
For mining companies looking to optimise their operations, adopting a strong reconciliation framework at every stage is essential. It not only improves operational efficiency but also ensures that projects are executed with accuracy, reducing risks and maximising returns.
If you want to know more about this topic, feel free to reach out to Rayleen Hargreaves. You can contact her here.
Related Posts
We provide a lot of great technical content for free!
Subscribe here for our podcasts, technical articles and news