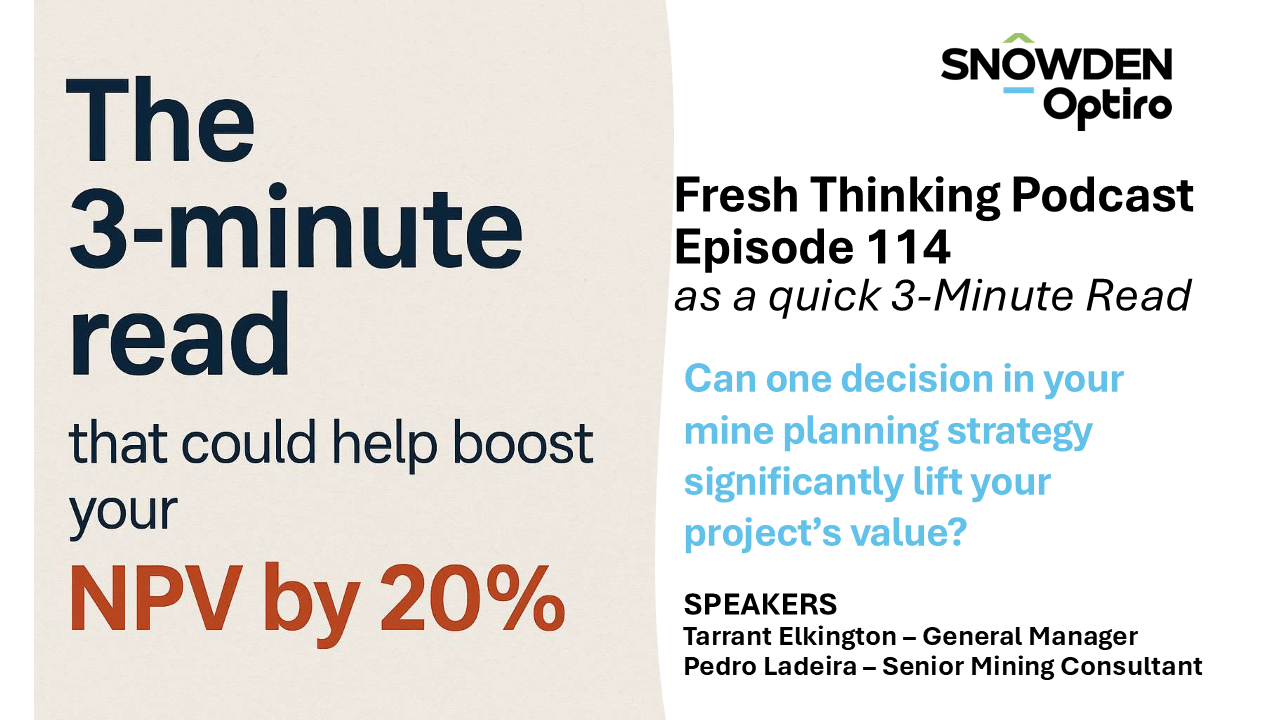
- news
Planning For the Average Is Planning To Be Average – Part 2
Tarrant Elkington General Manager at Snowden
In my last article, I talked about the fact that there is a lot of value left on the table by failing to model relationships in your optimisation input parameters. That, by planning for the average, you are planning to be average.
Let me share with you a published example where we used some trends, supported by testwork, to significantly improve project value. The Dutwa nickel laterite project in Tanzania was the subject of a paper by Elkington, Lorenzen and Czerny (2013).
The project was contemplating an atmospheric leach to produce a mixed hydroxide precipitation. These projects tend to have high processing costs, largely driven by acid consumption.
At around 1% Ni, project head grades were not particularly high, so beneficiation was considered important for project development success. Initial testwork identified that scrubbing primary crushed ore, with coarse rejection, offered a significant upgrade opportunity. Once a flowsheet was selected, a number of variability samples were tested (Figure 1). It identified:
- A strong proxy for beneficiation performance (Si head grade). A proxy that can then be used to help with ore/waste decisions, and in the margin ranking of blocks.
- That both deposits performed similarly through the beneficiation circuit, allowing them to be treated as a single metallurgical domain.
Figure 1 Ni upgrade factor as a function of Si head grade

- While the beneficiation upgraded all the acid consuming elements (Al, Fe, Mg), only Al upgraded by more than nickel (Figure 2). This meant that acid consumption per unit of Ni would drop as a result of beneficiation.
Figure 2 Upgrade factors as a function of Si head grade

Contrasting this to the typical approach of developing a composite for each rock type and applying average upgrade factors, we were able to code blocks with beneficiation performance and use Si as an important value driver.
In addition to understanding beneficiation performance, there was a work completed to understand the leach performance.
Firstly, a stochiometric model was developed to approximate the acid consumption as a function of leach grade composition. This flowed through into the ability to model the variability in processing cost per block. Given the high cost of acid, there was significant variability in cost, meaning that project value would not only be driven by Ni content but the ability to minimise acid consumption. This powerful model enabled a completely different mine plan to be developed to exploit the knowledge gained through the testwork.
Secondly, rather than simply taking the highest recovery result, Ni extraction versus acid consuming element extraction relationships were plotted (Figure 3). Results indicated a strong correlation of extraction of all elements as acid is added to the feed. In particular, at lower Ni recoveries there was low recovery of Al and Fe but high Mg recovery. As acid is added and Ni recovery increases, Al and Fe are recovered at an accelerated rate compared to Mg. This indicates there may be an opportunity to reduce acid. While this would further reduce the Ni recovery of the project, it would potentially allow a greater nickel production rate for a fixed acid capacity, given that acid consumption is reduced by more than Ni loss.
Figure 3 Relationship between Ni and Mg, Al and Fe leach extraction

Putting this together into the mine plan we were able to drive some positive economic outcomes.
Three cases were considered:
- Case 1 – no beneficiation and maximised nickel leach extraction
- Case 2 – beneficiation and maximised nickel leach extraction
- Case 3 – beneficiation and optimised (lower) nickel leach extraction
All scenarios considered a fixed acid constraint which meant that beneficiation feed and leach feed tonnes were able to vary.
In each case, the schedules were optimised using Snowden’s Evaluator software which maximises NPV over the LOM for a given set of economic and technical parameters and constraints.
The results shown in Table 1 demonstrate that the addition of beneficiation increased the discounted cash flow (DCF) by 13% and the economic leaching added a further 2%. The increases in value came despite a significant reduction in recovered nickel 1. It is important to note that the decrease in recovered Ni and hence revenue was surpassed by a larger reduction in project operating costs. And this is without consideration of the potentially lower capital costs associated with significantly lower leach feed.
Table 1 Summary of scenarios

The leach feed schedule (Figure 4) illustrates an interesting comparison. All cases show a declining leach feed rate, indicating the acid consumption increases over time. Case 2 shows a significantly lower leach feed rate as ore beneficiation increases the unit ore feed acid consumption of the accepted fraction. However, the nickel leach grade was significantly higher which allowed more Ni to be produced annually (Figure 5). In Case 3, the leach feed tonnes were able to increase as acid was reduced on a unit basis whilst still having a Ni leach grade higher than Case 1.
Figure 4 Leach feed schedule comparison

Figure 5 Leach nickel grade schedule comparison

Overall, with each case it was possible to increase the amount of recovered nickel, and revenue, for a fixed acid consumption (Figure 6). This came at the price of reducing mine life.
Figure 6 Recovered nickel schedule comparison

However, as can be seen from the cumulative discounted cash flow curves, that discounting reduces the value of later mine periods significantly. So, the increased revenue in earlier periods more than compensates for shortened mine life.
Figure 7 Cumulative discounted cash flow schedule comparison

By planning for orebody variability in this study, rather than planning for the average, it was possible to identify value levers that would not otherwise have been considered. It was definitely one of the more interesting studies with which I have been involved and I look forward to the next opportunity to work with datasets like this.
In my opinion, to be a really good mine planner you must not only be an expert in mine design and scheduling, but you should also understand the entire valuation process system and those value drivers you can leverage. You need to be an investigator and not just accept the first inputs provided. A change to the input relationships can make a bigger difference than any other mine planning process. Planning for the average is planning to be average.
Look out for future posts where I will delve into the world of strategic mine planning and optimisation, apply some of these topics, provide some tools and tricks and identify some of the big unsolved problems you might never have thought of. Please provide feedback, ask questions, and share your own experiences.
Thanks to Geoff Booth, Matt Mullins and Matt Cotterell for their review and feedback on this article.
Reference
Elkington, T., Lorenzen, L. and Czerny, C. (2013). The use of Geometallurgical Relationships in Process Route Selection and Mine Plan Optimisation for the Dutwa Nickel Project. The Second AusIMM International Geometallurgy Conference, Brisbane, pp. 207-216.
Related Posts
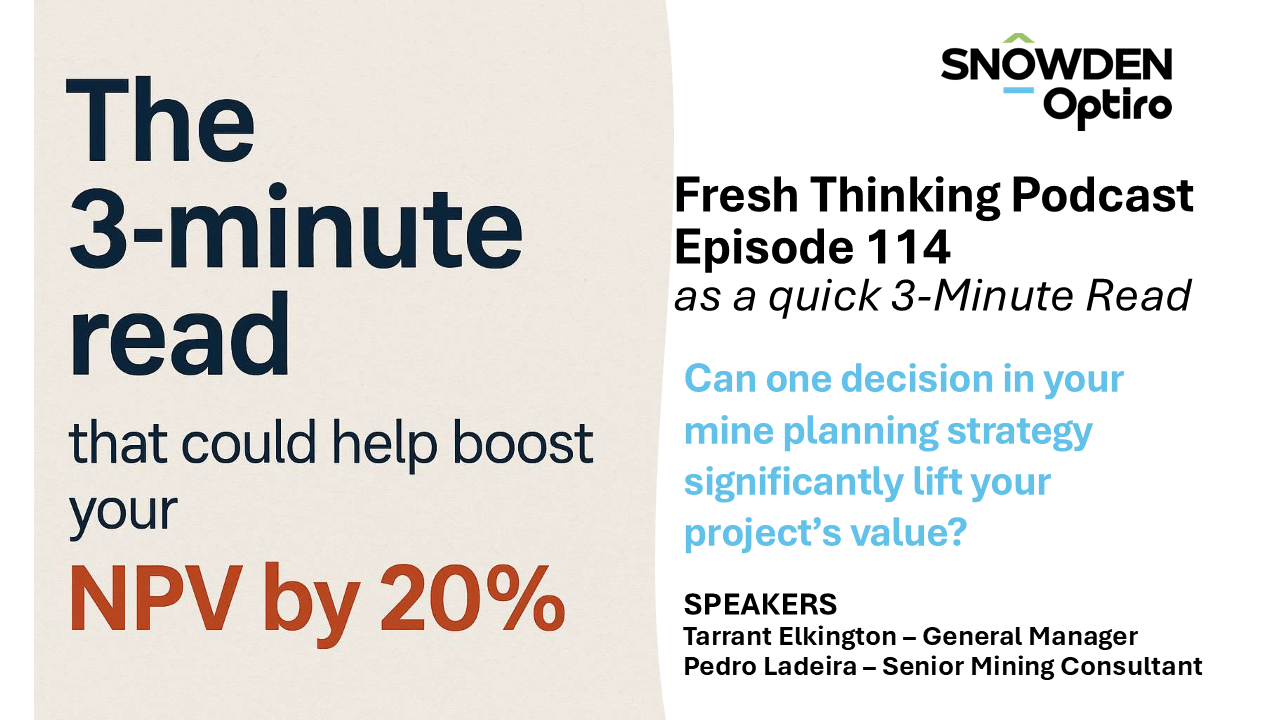
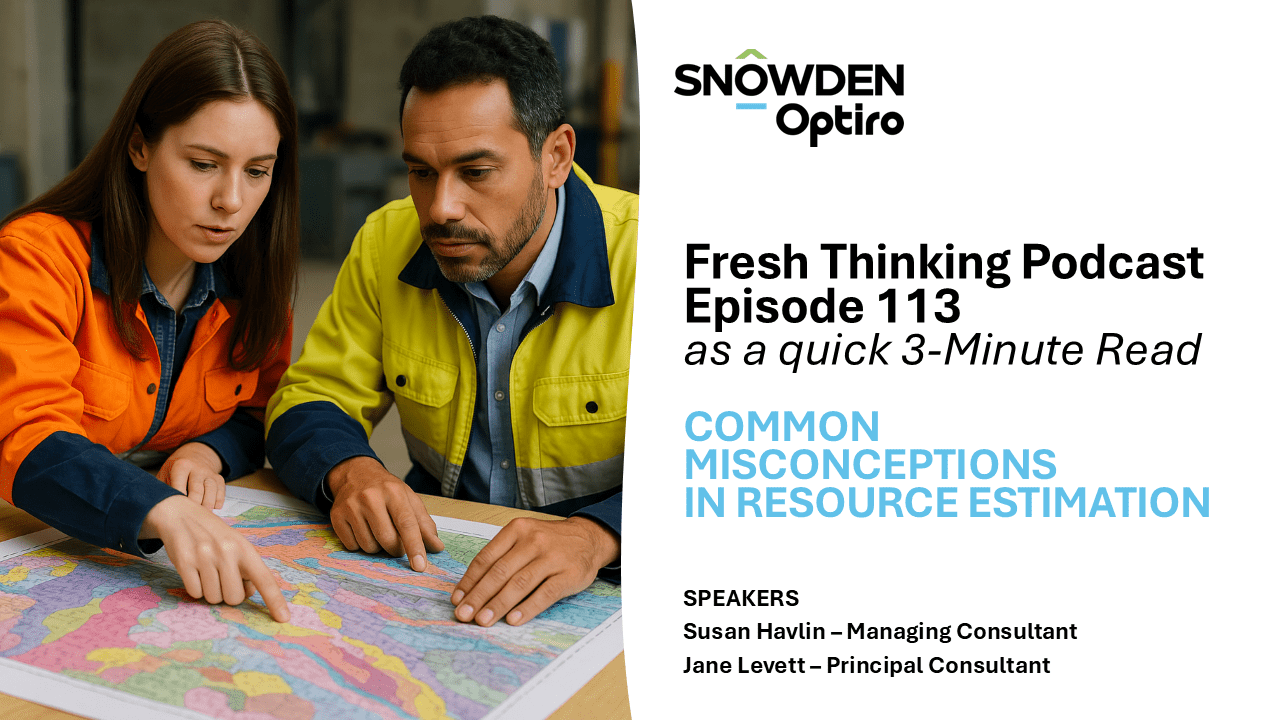
Fresh Thinking: The 3-Minute Read. Episode 113
We provide a lot of great technical content for free!
Subscribe here for our podcasts, technical articles and news