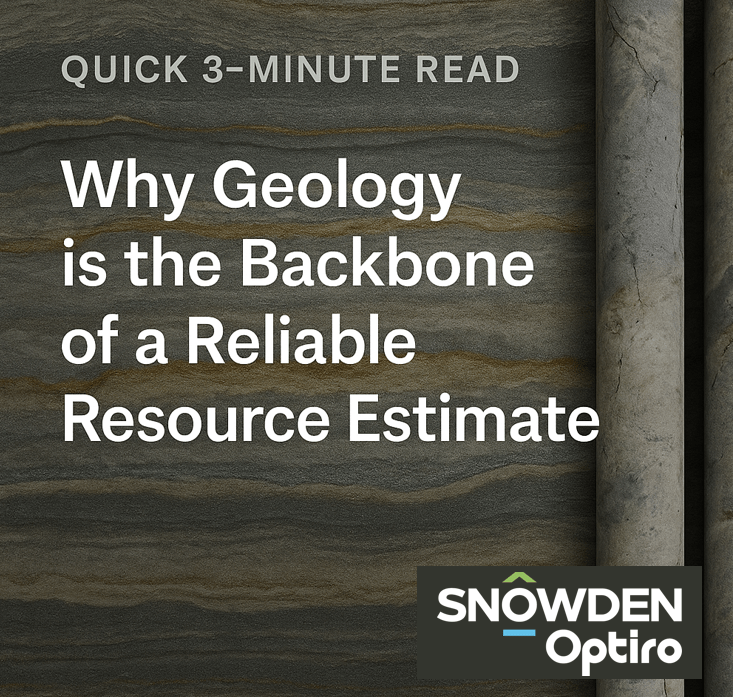
- news
Planning For the Average is Planning to be Average – Part 1
Tarrant Elkington General Manager at Snowden
In an earlier post I talked about the importance of the block value calculation and how it is the heart (and mind) of mine optimisation. Here is the simple (and brilliant) formula:
BV = [(P-S)RG – H]O – MT
Where:
BV = Block value in $.
P = Commodity price in $ per recovered metal unit
S = “Selling cost” in $ per recovered metal unit
R = overall metal recovery (fraction)
G = block grade
H = “Process cost” in $ per ore tonne
O = Ore tonnes
M = “Mining cost” in $ per rock tonne
T = Rock tonnes
With only a few key inputs you can calculate the value of a block of material. Add them up for all the blocks you are planning to extract and you get a good idea of the overall net cash flow of a mining project or valuation (excluding capital and the time value of money)[1]. Sounds too simple to be true doesn’t it?
Mining professionals often think that the use of averages in these inputs will suffice. Anything else is just too hard to figure out or not necessary. Taking the “lazy” approach of applying the average inputs for everything is OK, if all you want to get is average production and financial results and willing to deal with variation in outcomes as actual variability is revealed in operations. However, if you want to truly optimise a mining project you will go the extra mile to develop the input relationships.
The framework presented above can cater for a wide range of input relationships. Every input can be a function of any characteristic you know about each block; its weathering, lithology, hardness, grade, location… the list goes on. You are only limited to the data you have collected and your determination to spend the time (and budget) to uncover these relationships. In reality, each block will have a range about the mean block value.
The dance of the mine planner and the metallurgist
A few years back I participated in multi-disciplinary workshop for a mining project. During this session, the results of a metallurgical testwork program were presented. Some 40 samples of all different rocktypes and grades reviewed. My curiosity was piqued when I realized that this test work could be used to add value to the mine plan.
To my dismay, the metallurgist concluded that the average results from the testwork program simply confirmed the process design criteria and that was that. I asked whether there were any trends in the data to which the answer of “no” came back quickly, perhaps without adequate consideration. So, I asked to see the data. Within five minutes, it was clear that there was a near perfect relationship between one of the input grades and metallurgical performance. As it turned out, that relationship made perfect sense when considering the mineralogy of the deposit.
I get it. Metallurgists are looking to fix the process design criteria and this is easiest when you assume that you will get a single homogenous feed, allowing for the minimization of plant capital costs. But (a) is it realistic (or cost-effective) to assume an average life of mine blend? and (b) will planning for the average actually maximise the value of the project? The answer to both questions is almost always a resounding “NO”. Deposits are inherently variable. Thus, a plant design that does not account for such variability will inevitably be sub-optimal.
Those that do not understand the entire technical and economic mining system will “want to have their cake and eat it too”: an average blended grade that maximises value. But a blended grade often leads to a fixed revenue which, in turn, eliminates the most important value lever. To maximise NPV, IRR and minimise payback, you need to focus on your best material first. This often means higher grades, and higher recoveries in the first few years. This benefit will usually surpass (often significantly) any increased costs to access this better material or the capital costs to manage any feed variability. When revenue is fixed, all you can do is minimise cost, and there is a limit to the extent to which you can do this.
The disconnect between strategic mine planner and metallurgist can be frustrating. This is how it often goes. Mine planner asks for metallurgical relationships but is given fixed parameters for recovery, throughput, and cost. Mine planner develops mine plan which prioritises high grades and shows declining grades. Metallurgist freaks out because the plant was not designed to handle the higher grades and asks the mine planner to moderate the grades to suit the plant design.
So, as mine planners, how do we tease out these relationships that some metallurgists are not always keen to pursue? Firstly, we should start by asking the metallurgist:
- What ore characteristics impact on throughput?
- What ore characteristics impact on recovery?
- What ore characteristics impact on costs?
You might get a direct “no” or “we don’t have enough information to assess that”. This is when you need to try a little harder and ask some specific questions. Let’s work through some scenarios:
- It may well be that the recovery is based on the grade of a particular composite. A common question that can help is to ask the metallurgist if the recovery of the low-grade stockpile will be the same as the high-grade feed. If the answer is “no” then there is probably a grade-recovery relationship to be uncovered.
- Perhaps the average recovery requires a certain blend of grades or material types. Blend it this way and you can get the target recovery. This is often code for “one rock type has a higher recovery than another” but we don’t yet have the data to quantify the extent of the different. So, then is assuming the same recovery for each material type the best possible assumption we could make? Not really. OK, then can we try to make the best possible assumption instead?
- With throughput, let’s go to the extremes and ask “what if we put 100% oxide through the plant? What would the throughput be?”. OK, now what about 100% fresh?
- With cost, does oxide and fresh material have the same reagent consumption? And power consumption?
Usually, the issue with developing these relationships (particularly for a new project) is a lack of data to support a definitive relationship and the expense to generate the data. A significant amount of judgement is required on behalf of all experts. One thing that is often forgotten is that a fixed average number is also an assumption, and will often be more misleading than to assuming a relationship between variables.
It is important to note that it is not just about the metallurgist. The mine planner should also look in their own backyard and make sure that they are modelling throughputs and costs appropriately based on location and rocktype. Are you modelling costs, and trucking throughput by pit location and rock type? Are you modelling drill and blast costs based on the material characteristics? Have you captured dilution and ore loss on a local rather than global basis?
The next time you see a set of input parameters filled with average numbers, just remember that planning for the average is planning to be average. In Part 2, I will share a case study.
Look out for future posts where I will delve into the world of strategic mine planning and optimisation, apply some of these topics, provide some tools and tricks and identify some of the big unsolved problems you might never have thought of. Please provide feedback, ask questions, and share your own experiences.
Thanks to Geoff Booth, Matt Mullins and Matt Cotterell for their review and feedback on this article.
[1] I am going to park the issue of non-additivity of variables until a later post.
Related Posts
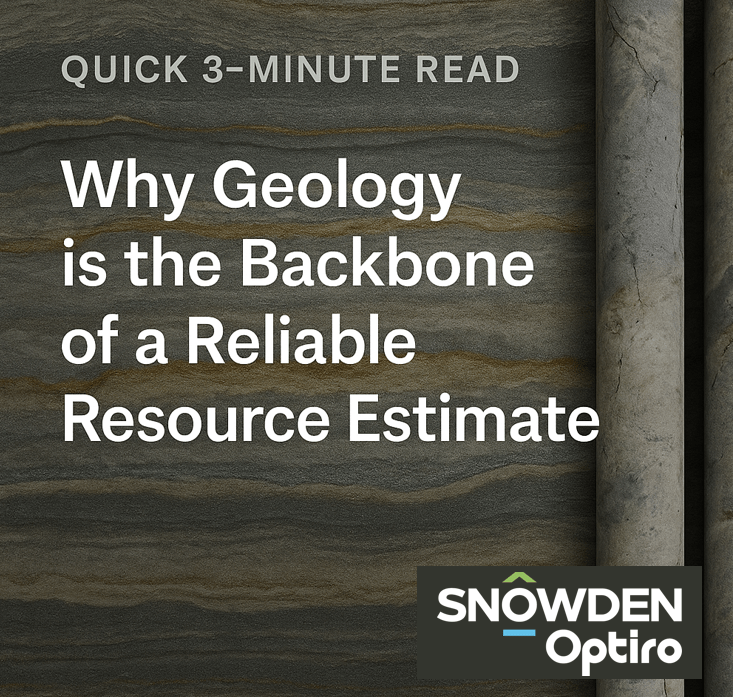
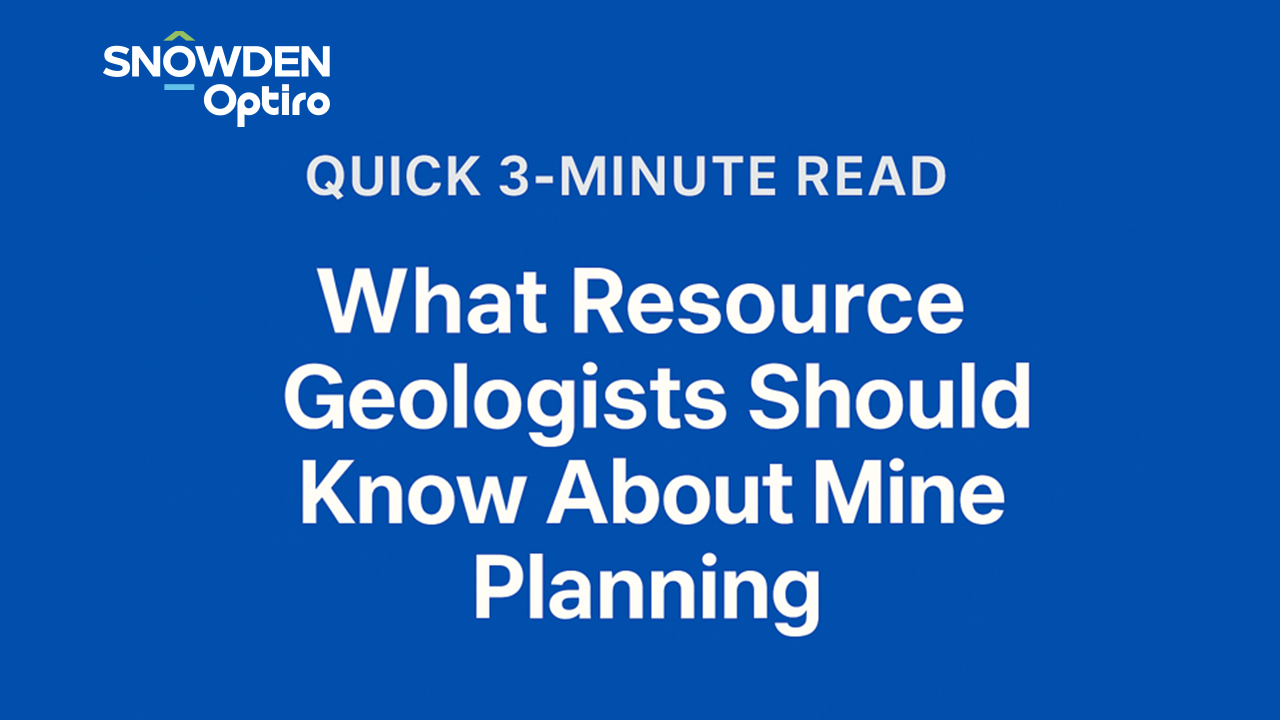
Fresh Thinking: The 3-Minute Read. Episode 115
We provide a lot of great technical content for free!
Subscribe here for our podcasts, technical articles and news