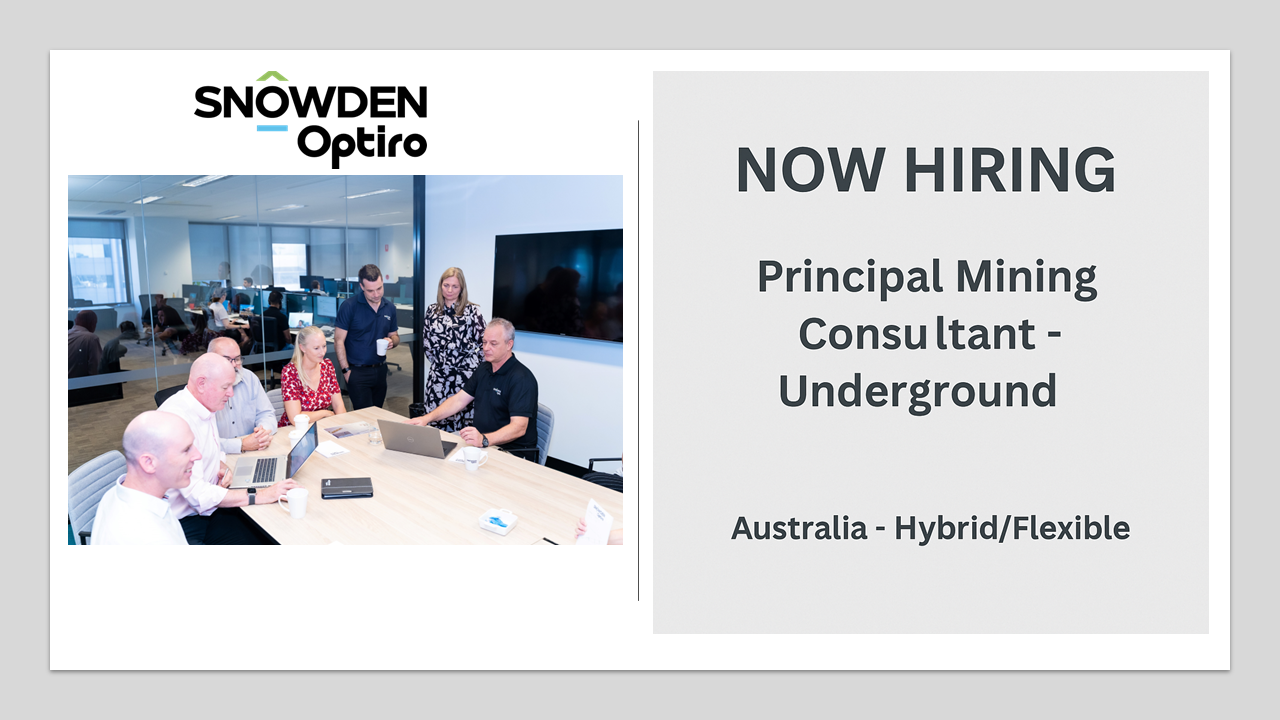
- news
Fresh Thinking: The 3-Minute Read. Episode 107
Here’s your 3-minute quick read of Fresh Thinking by Snowden Optiro’s podcast Episode 107.
We’ve pulled out the key insights and takeaways—perfect for when you want the value, minus the headphones.
Fresh Thinking: Refractory Gold – What Makes It So Challenging?
In this edition of Fresh Thinking, Snowden Optiro’s General Manager, Tarrant Elkington, sat down with metallurgical engineer Dr Leon Lorenzen to unpack one of the more complex challenges in gold processing: refractory and semi-refractory gold ores.
Dr Lorenzen, who brings over 40 years of experience in operations, research, and consulting, offers valuable insights into what makes some gold ores harder to treat—and why it matters for both miners and investors.
Their discussion covered the following:
What is Refractory Gold?
The term “refractory” is relative but generally refers to gold ores that do not respond well to conventional leaching techniques. If standard processing doesn’t yield sufficient gold recovery—usually less than 90%—the ore is considered semi-refractory. Below 80%, it’s refractory, and below 50%, very refractory.
Why? The gold in these ores is often encapsulated in other minerals such as pyrite, pyrrhotite, chalcopyrite, or bound up in carbonaceous material or silica, making it physically or chemically inaccessible without additional treatment.
Spotting the Signs Early
Early detection is key. Geologists and metallurgists can often identify potential issues during exploration and domain modelling—especially when fresh, sulfide-rich zones are observed. From there, metallurgical testing helps confirm whether more advanced processing will be needed.
The Cost of Complexity
Refractory ores have a major cost implication. Because they require additional processing steps like oxidation, ultra-fine grinding, flotation, or pressure oxidation, both capital and operating costs increase significantly.
Some operations accept lower recovery (e.g., 82%) to avoid high processing costs, while others invest in more intensive approaches to maximise return—this choice depends on detailed financial modelling.
Processing Options: One Size Doesn’t Fit All
There are five main processing routes commonly used for refractory gold:
- BIOX (bio-oxidation): effective for arsenopyrite-rich ores
- POX (pressure oxidation): capital intensive, but powerful
- Albion Process: good for certain sulfide ores; requires significant space and neutralisation
- Roasting: less common in Australia due to environmental impact
- Ultrafine Grinding: works when gold isn’t too tightly locked
Each comes with its own energy, reagent, and infrastructure requirements, and ore mineralogy largely dictates the best fit.
What’s Ahead for Refractory Processing?
While not widespread today, more refractory processing plants are on the horizon. Examples already in operation include BIOX plants in Tasmania, Victoria, South Africa, and major projects like Lihir and Siguiri. The Grassy Hill project is expected to use POX, and Glencore continues to implement the Albion process across several sites.
As processing technology evolves, centralised hubs for treating refractory ore from multiple sites may become a cost-effective solution—especially for underground mining operations where higher grades can offset the complexity.
Want to hear or watch the full podcast?
Catch the full conversation on YouTube or the audio podcast on Spotify – and don’t forget to Subscribe for more Fresh Thinking.
If you would like to contact either Tarrant or Leon: contact@snowdenoptiro.com
Here is a LINK to our Snowden Optiro YouTube channel.
Related Posts
We provide a lot of great technical content for free!
Subscribe here for our podcasts, technical articles and news