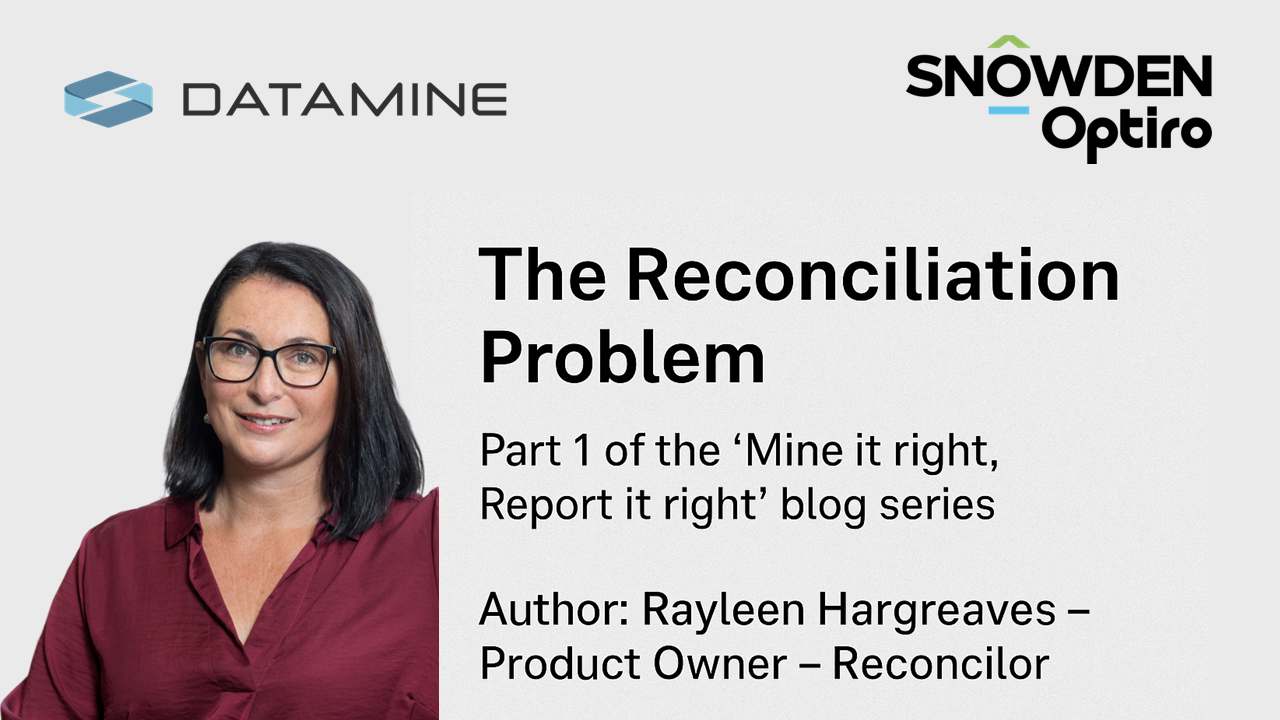
- Uncategorized
Mine Planners: Are You Looking At The Drillholes?

Author: Tarrant Elkington, General Manager
I was recently reading an old article by Julian Poniewierski called Mining Engineers – Are you Taking Suitable Interest in the Reserve Reconciliation?” Great read and recommended. It reminded me of another important consideration that mine planners do not often take an interest in: the drillhole data.
Viewing drillhole data would be seen by many mine planners as, what I would call, an “SEP” (someone else’s problem)”. After all, the drillhole data was used to create the block model; why would I need to care? For many years this was my view; it made my life easier! That was until one particular project a few years ago
I was working on a scoping study and developing a conceptual mine plan. While I was reviewing the pit optimisation to determine the stage the metallurgist called asking for the drillholes to do some metallurgical testwork planning. I asked the geologist for these (not from Snowden I will add). And when I received them, I was astonished. I knew there were only about 10 drillholes in the area and appreciated that it the project was at an early stage. What I didn’t know was, that there was only one drillhole in the vicinity of the pit shell. And that drillhole was supporting the entire 15 year mine life! The other holes were all further along strike and not included in the model. As you could imagine, at that point, the thought of optimising the cutback design on the model provided seemed a bit pointless. Of course, there is not much as a mine planner you can do in this situation with the information. But it does help to set the context of the mine plan you are creating.
In case you were wondering, further drilling did largely confirm the resource as modelled. Nonetheless, it gave me a scare and made me wonder why I didn’t just routinely look at the drillholes as part of my work. And that led to a range of other learnings and understandings around the way resources are modelled. Let me share a couple of these with you.
WHAT IS YOUR PIT DRIVING ON?
Do you ever look at the drilling against your pit optimisation or pit design? Pit optimisations are completed on models and often the pits will drive on higher grade areas within the model. But how supported are those model areas? See an example in Figure 1 showing the block model, optimised pit and the supporting drilling on the section. Perhaps the drillhole spacing has gaps in the area your pit is optimising (or the pit optimised on an area between drillholes). Or sometimes the method of modelling the resource is such that there is influence from off-section or up/down dip samples, or very high grades that estimate a grade in a specific block that has some local uncertainty. After all, resource models are still models. And like all models, all of them are wrong but some are useful. As mine planners, it simplifies our life to believe that the resource model is exactly right, but all good geologists will tell you that they are estimates and only as good as the underlying data practitioner’s skill.
FIGURE 1: Model and drillhole comparison example (with pit shell)

Viewing the drillholes in the context of a pit optimisation provides some interesting feedback to resource geologists about areas within often very large and complicated deposits, that need special attention. Break down the silos to pursue a better outcome.
Similarly, the underground mine planning processes would benefit from reviewing the stope designs against the drilling. Perhaps you designed a beautiful stope that has no drilling within it, or near it.
UNDERSTANDING LOCAL GRADE VARIABILITY
Many resource models (and I will not get into the methods) implement smoothing of the drill data to create a resource model, effectively damping the local variability to produce a less biased estimate of grade.
Often I hear from the geologists when discussing grade control strategies “but what about the local variability? You will need really close spaced grade control drilling”. And, as a mine planner looking at the block model you respond with “what local variability?” Figure 2 shows a deposit has been modelled into reasonable large block relative to the variability in the drill holes producing a somewhat smoothed model. Probably fine globally but does not necessarily reflect the local variability seen in the drilling. In reality, the deposit will likely look more like that in Figure 3, although we cannot be confident about the grades of those blocks locally.
FIGURE 2: Smoothed estimate example

FIGURE 3: Simulated model estimate

The mine planner is being obscured from the true variability of the deposit with the first example, and risk (and opportunity) created by that variability. This can lead to poor decisions around production rate, cut-off grade strategy, equipment strategy, dilution and ore loss estimate and grade control strategy i.e. pretty much everything the mine planner does. This is not to blame the resource geologist in any way. It is just a function of the standard modelling approaches and the density (or sparsity) of data. More advanced estimation methodologies are attempting to address this apparent variability mismatch but introduces their own issues that I might talk about in a later post. However, a quick look at the drilling can reveal issues that the mine planner can take these into consideration in their work.
There will be heaps of other examples where a mine planner’s understanding of the drilling would improve mine planning. Please share any from your experience in the comments.
I think the most important thing that came from looking at the drilling was to gain a greater appreciation of the complexities in resource modelling, to learn why certain modelling methodologies produce certain deficiencies the mine planners should be aware of.
Comparing the model to drillholes uncovers questions that improve deposit understanding and lead to better strategic decisions. Being a better mine planner isn’t just about the mine planning. It is becoming more and more about understanding and challenging the inputs you get. After all, the mine planner has the keys to unlock a lot of value. And with those keys comes responsibility.
I must admit that I don’t always follow my own advice. Sometimes the drillholes are not in the right format for the software I use, or sometimes time just gets away from me. However, I will often think back on those projects and wish that I had looked at the drillholes to improve my understanding.
Bottom line… Look at the drilling, ask questions, and make better strategic decisions.
Look out for future posts where I will delve into the world of strategic mine planning and optimisation, apply some of these topics, provide some tools and tricks and identify some of the big unsolved problems you might never have thought of. Please provide feedback, ask questions, and share your own experiences.
Related Posts
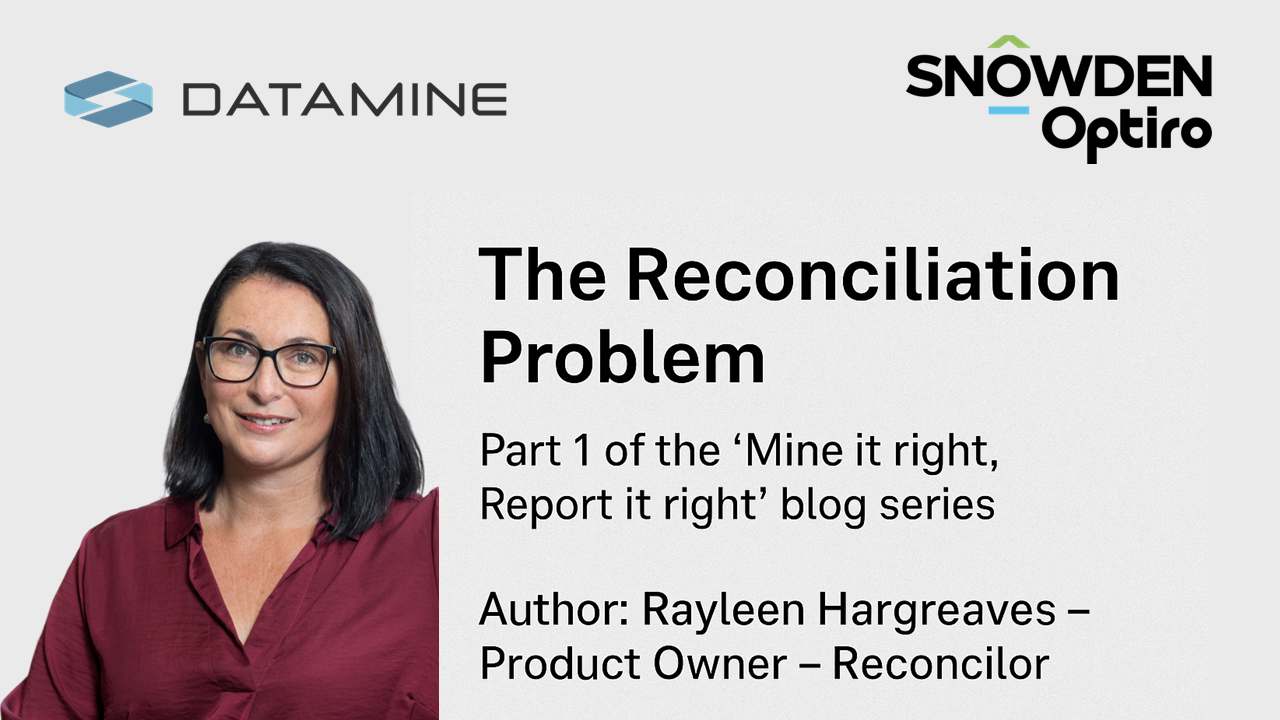
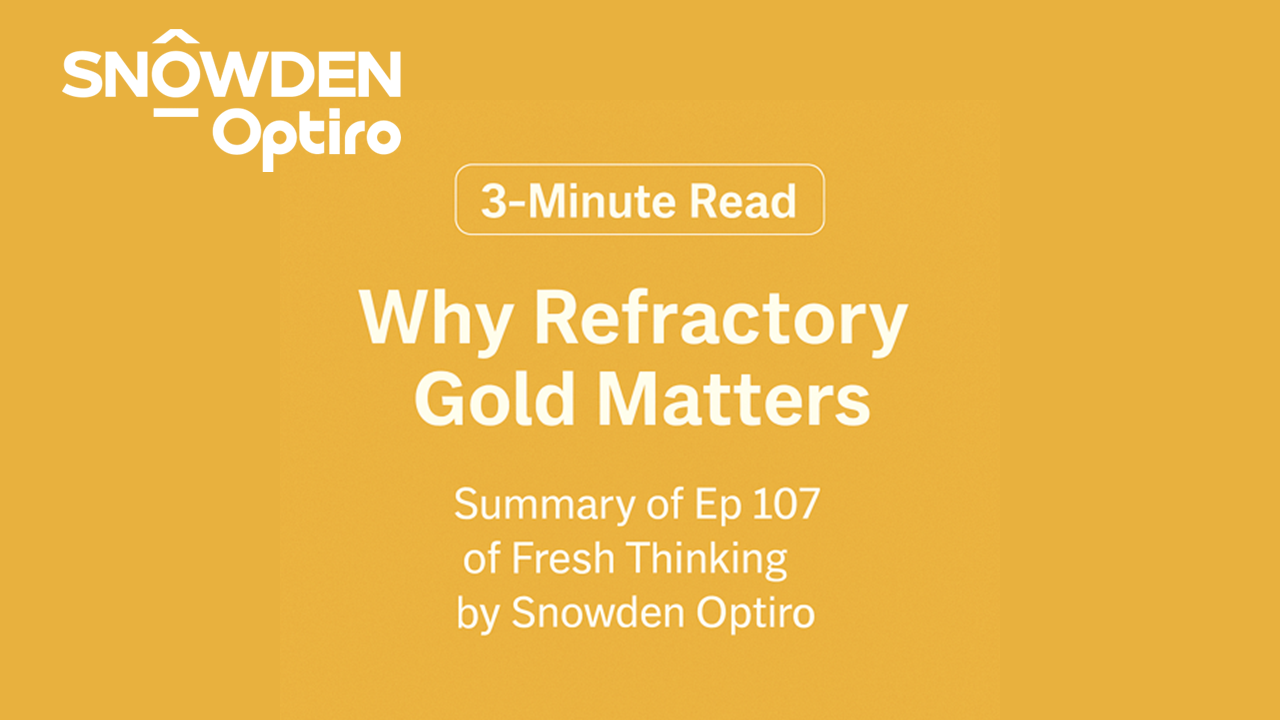
Fresh Thinking: The 3-Minute Read. Episode 107
We provide a lot of great technical content for free!
Subscribe here for our podcasts, technical articles and news